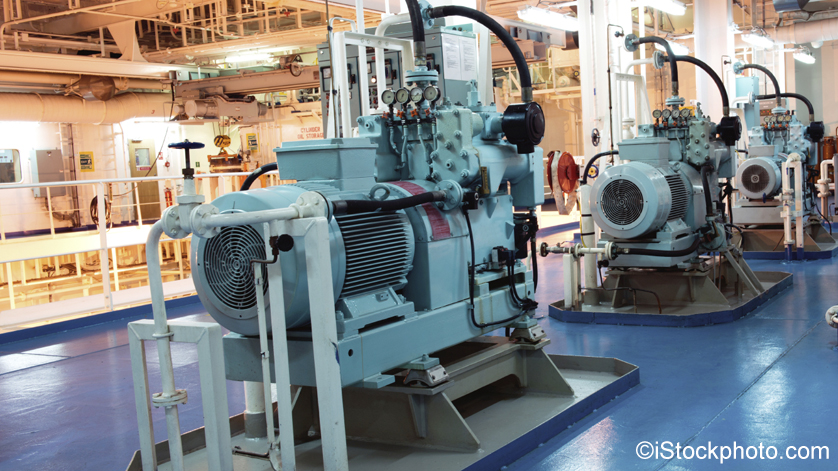
La mesure de pression est une partie intégrante du process de contrôle pour comprendre comment un compresseur d’air fonctionne en continu de manière économique.
L’augmentation du coût de l’énergie signifie que chaque unité au sein d’une usine doit toujours fonctionner avec des performances optimales, et pour les compresseurs d’air il s’agit d’augmenter ou de diminuer la charge du compresseur pour répondre à la demande changeante de l’air comprimé à travers les lignes de l’usine.
D’ailleurs il devient de plus en plus courant d’installer des systèmes de «gestion de l’air», qui surveillent les indicateurs de performance ainsi que toutes les étapes des différents compresseurs d’air reliés au réseau d’alimentation en air comprimé – en faisant en sorte que chaque compresseur fonctionne à un niveau de puissance exact et juste le temps nécessaire. Pour le faire efficacement, des capteurs de pression sont nécessaires pour surveiller la pression de sortie de chaque étage de compression, ce qui implique quelques défis :
- Les compresseurs d’air sont sujets à de fortes vibrations, ce qui signifie qu’un capteur de pression installé directement sur le corps d’un compresseur est soumis proportionnellement à des niveaux élevés de vibration. Cela peut conduire à l’échec de nombreux capteurs de pression installés de telle manière, sauf si ils sont pré-conçus pour ces environnements de travail exigeants.
- Un autre problème majeur rencontré par les capteurs de pression installés sur les compresseurs d’air est la température ambiante élevée – les pièces des compresseurs et leurs jeux mobiles très serrés entraînent une augmentation de la température à l’intérieur du corps, ce qui peut amener des erreurs sur le signal de sortie du capteur de pression liées à la température qui conduisent à des calculs inexacts de puissance.
Les concepteurs de compresseur ont trouvé une solution pour régler ces problèmes : l’installation de capteurs de pression (et d’autres instruments similaires) à distance sur un panneau latéral à côté du corps principal du compresseur – l’exposition à la fois aux vibrations et aux températures ambiantes élevées sera ainsi réduite, et le capteur de pression sera protégé contre les effets nocifs de ces conditions. Avoir un capteur de pression compact avec un double filetage au raccord pression (un filetage extérieur pour fixer le capteur sur le panneau latéral, et un filetage interne pour se connecter au tuyau d’air) est un outil utile lors de la conception d’une telle solution. C’est exactement ce que WIKA propose avec le C-2 – LE capteur de pression pour compresseurs d’air. Découvrez toutes les caractéristiques de ce capteur sur notre site.