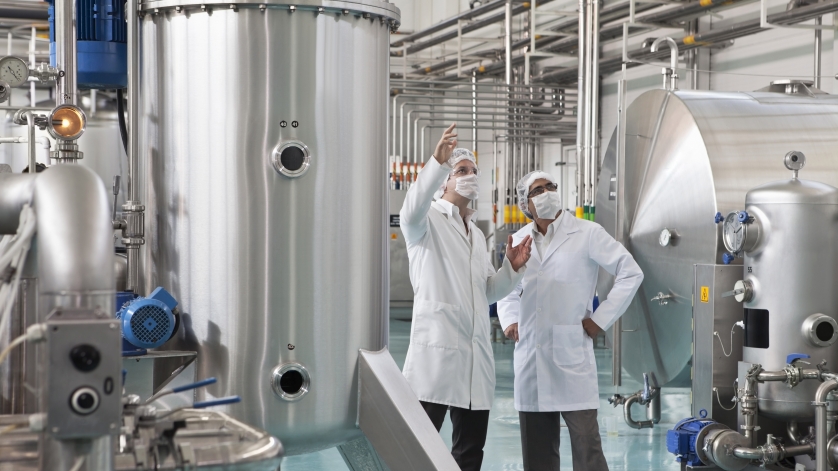
La surveillance du niveau de liquide par la mesure de la pression différentielle est entrée dans une nouvelle dimension : un système possédant deux transmetteurs de process dans un montage maître-esclave. Comparé aux solutions de mesures traditionnelles, cette configuration bénéficie d’une installation facile, d’un effet de température diminué et d’une précision accrue.
Concernant la surveillance des niveaux de liquide, le marché propose de nombreuses méthodes différentes. Dans les applications impliquant des cuves fermées ou des conteneurs similaires, le niveau est souvent déterminé en utilisant un transmetteur de pression différentiel. Cette technique, qui a fait ses preuves, convient à de nombreuses situations, notamment lorsque l’utilisation d’un instrument de mesure immergé est impossible, par exemple en raison de l’installation d’une broyeuse ou de la présence d’une substance agressive dans le conteneur.
Afin de surveiller le niveau, la pression différentielle doit être déterminée entre les phases liquide et gazeuse à l’intérieur de la cuve. Afin de permettre le calcul précis du niveau, outre la pression hydrostatique, la géométrie de la cuve (horizontale, verticale, différents couvercles et fonds possibles) et la densité du produit spécifique doivent également être prises en considération.
Les transmetteurs de pression différentielle possèdent deux connexions 1/4” NPT disposées l’une à côté de l’autre conformément à la norme CEI 61518. Ce concept reflète la mission de mesure unique de l’instrument, à savoir déterminer une baisse de pression, par exemple dans les tuyaux, les filtres ou les pompes. Lors de la mesure des niveaux de liquide, d’un autre côté, la distance entre les points de mesure pour les pressions P1 et P2 est beaucoup plus importante et doit par conséquent être pontée à l’aide de capillaires. Celles-ci possèdent un volume limité afin d’assurer la transmission de la pression sans interférence. Les solutions de mesure possédant ce type de connexions vers les points de mesure sont sensibles aux effets de température qui impactent les résultats. Dans le pire scénario, des variations sévères de températures pourraient fausser la valeur mesurée.
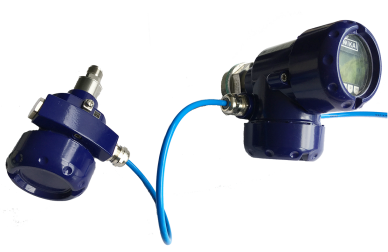
Ces deux appareils fonctionnent selon le modèle maitre-esclave
La solution maitre-esclave
Si l’application nécessite une haute précision, alors cette méthode de mesure atteint très vite ses limites. Dans le même temps cependant, une solution alternative existe et réduit les effets négatifs des mesures traditionnelles au minimum à l’aide de mesures de pression différentielle électronique pour surveiller les niveaux de liquide. Ce système de mesure développé par WIKA se base sur deux transmetteurs de process distincts : par exemple, CPT-2x ou IPT-2x, dont la précision atteinte équivaut jusqu’à 0,05 % du réglage de l’échelle, dans différentes configurations. Ces deux appareils fonctionnent selon le modèle maitre-esclave et disposent d’une connexion uniquement électrique via un câble à toute épreuve. Ils communiquent sur un bus interne.
L’esclave reçoit l’alimentation par le maître et est paramétré soit par les interfaces, soit sur l’écran de l’appareil maître. Il mesure la pression P1, par exemple, la pression du gaz dans une cuve fermée et transmets les résultats au maître. La pression P2, qui dans ce cas, est la pression dans la colonne de liquide au fond de la cuve, est contrôlée par le maître. Ce dernier calcule ensuite la différence de pression entre P1 et P2. Le volume de la cuve est déterminé par le maître comme indicateur du niveau basé sur cette différence et prend en compte d’autres paramètres de process clés tels que la forme de la cuve et la densité du produit. Cette valeur peut être transmise à la salle de contrôle et/ou l’écran de l’appareil maître en tant que signal analogique ou numérique.
Des avantages multiples
Cette solution n’a pas uniquement pour avantage de simplement diminuer l’influence de la température au minimum et de permettre une précision plus élevée. Les mesures de pression différentielles électroniques se mettent en place et fonctionnent également plus rapidement. En comparaison, un test de fonctionnement en amont avec un transmetteur de pression différentiel est essentiel dans la mesure des montages afin de s’assurer que les capillaires fonctionnent correctement, par exemple, en éliminant les poches d’air des tuyaux de pression et d’impulsion.
Il est également beaucoup moins complexe de remplacer les instruments dans le cas d’une mesure électronique de la pression différentielle. En outre, seul un de ces deux appareils doit être changé dans le cas d’un dysfonctionnement ; l’autre peut travailler avec l’appareil de remplacement (maître ou esclave). Lorsque la pression différentielle est mesurée à l’aide de capillaires, un défaut nécessite inévitablement un remplacement complet, même si un petit problème dans les tuyaux de pression est l’unique souci.
La méthode de mesure de pression différentielle électronique décrite ici pourrait théoriquement être également réalisée à l’aide de deux transmetteurs de pression. Cependant, ceci impliquerait l’installation d’un troisième composant avec une unité de calcul essentielle ainsi qu’une seconde source de tension et deux entrées de pression dans le montage de mesure. Les composants électroniques nécessaires au traitement de l’information et au calcul de la pression différentielle sont déjà intégrés au transmetteur de process.
De nombreuses applications de niveau de liquide bénéficient d’une option supplémentaire de transmetteurs de process, qui peut être désactivée afin de régler l’échelle individuellement. Dans le contexte des mesures de niveau de liquide, l’opérateur de la cuve met à l’échelle la plage de mesure du transmetteur afin qu’elle soit pertinente pour le process. Le signal de mesure, par exemple 4…20 mA, est ensuite utilisé de manière optimal dans cette échelle.
Dans le même temps, il ne faut pas oublier que la précision des mesures diminue proportionnellement si le transmetteur est éteint au-delà d’une certaine limite. Cependant, si cela ne dépasse pas 5:1, il n’existe aucune restriction sur l’utilisation de la fonction arrêt. Si le réglage de l’échelle couvre 200 mbar, (=2 m de la colonne d’eau), alors l’instrument de mesure peut être utilisé avec 0…1 bar sans affecter la précision de par exemple, 0,1 % ; à 200 mbar, la mesure de l’incertitude ne dépassera plus 0,2 mbar ou 2 mm.
Une polyvalence supplémentaire est ajoutée aux caractéristiques des mesures de pression différentielle électronique. Outre le contrôle effectif des niveaux de liquide, cette méthode est principalement dédiée aux applications possédant divers médias, par exemple dans la fabrication de jus de fruits, où le rapport de mélange entre le concentré et l’eau peut être déterminé sur la base de la densité et donc du changement de pression. Les bateaux en sont une autre illustration. Les réservoirs doivent être contrôlés en raison du mélange entre l’eau de mer avec d’autres fluides et lubrificateurs. La pression différentielle due aux densités de produit survenant dans les cuves se manifeste lorsque le niveau de l’eau atteint la limite maximum définie.
Avec ces caractéristiques de mesure, il devient évident d’utiliser également un montage maître-esclave pour les mesures de débit basées sur la pression différentielle, par exemple les filtres ou les plaques à orifice dans les pipelines. Alors que dans les cuves, les conditions de pression statique prévalent, les pressions de process relativement élevées sont la norme dans les tuyaux. Cependant, les différences de pression qui sont décisives pour ce type de mesure ont tendance à se situer dans la zone de quelques millibars. Afin d’être en mesure de contrôler la pression statique et de l’utiliser pour le calcul, les transmetteurs doivent par conséquent être conçus avec une plage de mesure beaucoup trop large pour les mesures en question. Ces mesures ne pourraient alors plus être considérées comme précises.
C’est pour cette raison que les transmetteurs de pression différentiels classiques sont conseillés pour la mesure du débit. Ils déterminent la pression différentielle basée sur la baisse de pression en millibars, tandis que la pression statique peut facilement atteindre 150 bar ou plus.
Conclusion
Un système de mesure de pression différentiel avec deux transmetteurs de process dans un montage maître-esclave élargit les options de contrôle des niveaux de liquide dans les cuves fermées ou les conteneurs avec des médias mixtes et une alternative extrêmement flexible. Il est principalement adapté aux applications exigeant une haute précision, où les effets de la température doivent être évités dans la mesure du possible.
SI vous souhaitez en savoir plus, n’hésitez pas à contacter votre responsable commercial habituel.