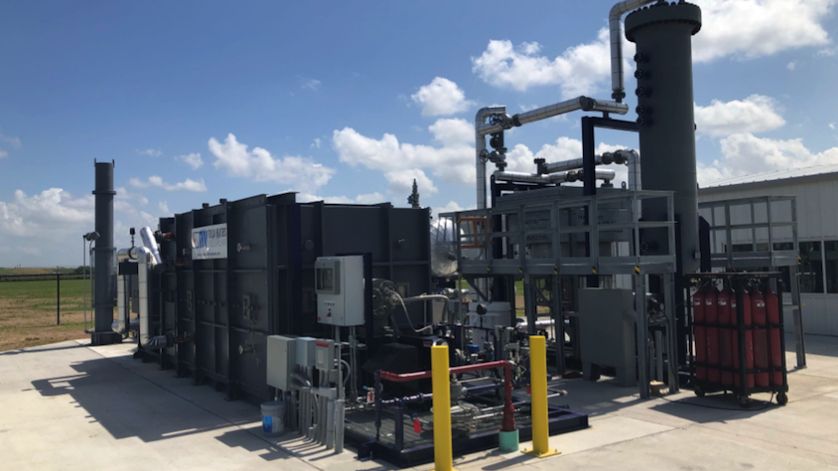
Même les meilleurs tests de laboratoire ne peuvent reproduire les conditions réelles, et les tests dans des process actifs sont parfois inefficaces, voire impossibles. Pour tester les instruments de mesure dans des conditions et des configurations spécifiques, WIKA USA a construit sa propre unité de traitement grandeur nature – avec un réacteur et un four à gaz.
Pourquoi WIKA a construit une unité de process à taille réelle
Les laboratoires de test et de développement de WIKA sont parmi les meilleurs du monde. Dans ces environnements contrôlés, nous testons soigneusement et méthodiquement nos instruments utilisés pour la mesure de la température, de la pression, du débit, du niveau et de la force. Dans certains cas, nous faisons appel à des instituts tiers pour valider nos résultats.
Cependant, les tests en laboratoire ne sont pas toujours suffisants. Pour certains process, un environnement simulé ne peut pas reproduire les conditions réelles.
Pour les instruments de température utilisés dans les usines de traitement, l’idéal serait de tester sur une unité active, même si les inconvénients rencontrés sont liés au temps, au coût et à l’aspect pratique. Les raffineries et les usines pétrochimiques doivent continuer à fonctionner pour rester rentables, et les arrêts doivent se limiter à la maintenance et aux réparations. Certains tests ont lieu pendant ces arrêts programmés ; en fait, certains tests d’instruments commencent pendant une révision (TA) et sont laissés en marche jusqu’à la prochaine. Le problème est que ces conditions spécifiques sont littéralement fixées pour le long terme, car les cycles de TA durent souvent quatre ans ou plus. Ce serait donc un test très long !
De plus, un test peut nécessiter des actions qui seraient inacceptables dans une situation réelle. Par exemple, des thermocouples trempés sont martelés dans de petits trous percés dans les parois des tubes de four. Ce procédé est parfait en laboratoire, mais le faire dans une unité de traitement active affaiblirait la paroi du tube et créerait des points de défaillance potentiels.
Pour tester correctement la gamme de thermocouples et les autres instruments de mesure de WIKA, nous avons trouvé une solution qui combine le meilleur des deux mondes : une véritable unité de process que nos ingénieurs peuvent démarrer, arrêter et manipuler selon les besoins – le tout sans gêner personne dans l’industrie du process.
Le centre de création et de test de WIKA
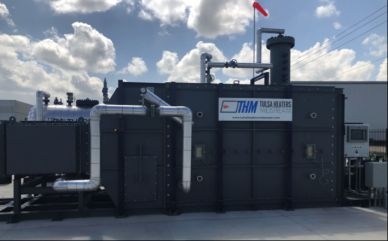
L’unité de traitement WIKA de Pasadena, au Texas, est entièrement fonctionnelle et se consacre aux essais d’instruments et à la R&D
Avant de mettre en place cette installation de test de classe mondiale, nos spécialistes ont passé des années à consulter de nombreux experts de l’industrie, des décideurs et des utilisateurs finaux. Après avoir recueilli leurs commentaires, nous avons lancé une initiative de plusieurs millions de dollars pour construire un campus de recherche et développement de 557 m² à Pasadena, au Texas, non loin des dizaines de raffineries situées au cœur du Houston Ship Channel. La pièce maîtresse de ce campus est une unité de traitement active de taille réelle qui a été conçue et construite conformément aux directives de l’ASME et de l’API.
L’unité, qui a commencé ses activités à la mi-2019, travaille avec des fluides allant des liquides aux vapeurs et aux fluides à phases mixtes. Il existe également un système innovant de parois de four qui peut s’adapter à presque toutes les conditions d’essai. Le four de 9,6 millions de BTU est capable de reproduire un large éventail de process qui ont lieu dans des fours et des réacteurs à plus grande échelle.
Cette unité de pointe permet à nos équipes d’obtenir des données réelles sur le portefeuille complet d’instruments de mesure de WIKA, y compris les produits ETM (mesure électronique de la température) suivants :
- Ensemble de thermocouples multipoints Gayesco Flex-R® ( type TC96-R)
- Thermocouple WIKA V-PAD®tubeskin (type TC59-V)
- Ensemble thermocouple Gayesco XTRACTO-PAD®tubeskin (type TC59-X)
- Ensemble thermocouple Gayesco REFRACTO-PAD®tubeskin (type TC59-R)
L’installation nous permet également de développer et de tester la prochaine génération d’instruments pour les raffineries et les usines pétrochimiques.
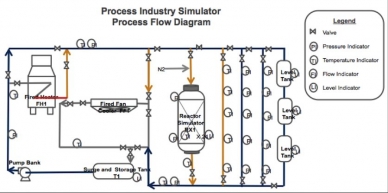
Tests dans une unité de traitement en condition réelle
Grâce à une unité de traitement grandeur nature et pleinement fonctionnelle, nous pouvons effectuer une variété de tests et de vérifications qui n’étaient pas possibles auparavant. En plus de soumettre nos instruments de mesure à des conditions de travail réelles, nous pouvons désormais recréer les problèmes que rencontrent parfois les unités de nos utilisateurs finaux – mauvaise distribution, points chauds et routage, pour n’en citer que quelques-uns – et voir comment ces conditions affectent les instruments ETM.
C’est ainsi que notre installation de test a été d’une valeur inestimable dans deux applications : la surveillance de
l’état des fours et le calcul de la dynamique des fluides.
Surveillance du conditionnement des fours
La surveillance de l’état des fours (SEF) est un processus par lequel les utilisateurs collectent des données sur place pour identifier les lacunes en matière de performance. Ils peuvent ensuite utiliser ces informations pour optimiser le positionnement des thermocouples et des assemblages de tubes et de gaines, ainsi que pour apporter d’autres améliorations opérationnelles afin d’améliorer les performances.
Avec la SEF dans l’installation d’essai, nous sommes capables :
- D’effectuer des évaluations terrain sur des conditions thermiques d’un four en utilisant des outils de diagnostic avancés, y compris l’imagerie infrarouge (IR) et d’autres instruments
- D’examiner les résultats préliminaires avec les spécialistes du four et de l’inspection du client, les responsables des opérations et d’autres personnes
- De publier un rapport sur les performances du four et nos recommandations
- De fournir une assistance et des conseils sur la sélection des thermocouples, des matériaux et de l’ingénierie pour une durée de vie optimale de l’unité
- De fournir et/ou superviser l’installation de capteurs de thermocouple tubeskin pour améliorer la surveillance de la température et la performance du four
- De mettre en place des programmes de surveillance pour les chauffages critiques
De plus, le campus de R&D est devenu un lieu naturel de formation pratique pour les clients qui souhaitent tirer le meilleur parti de nos instruments de mesure sur leurs propres unités de traitement. Ces meilleures pratiques sont le résultat de la SEF et comprennent la manière de :
- Augmenter la capacité des unités par l’optimisation et le déblocage des fours
- Améliorer l’efficacité énergétique grâce à une gestion optimale de la combustion du four
- Utiliser les évaluations de fiabilité pour réduire les arrêts non programmés
- Réduire les coûts d’entretien grâce à une meilleure planification de l’AT
- Dynamique numérique des fluides
Dynamique des fluides numérique
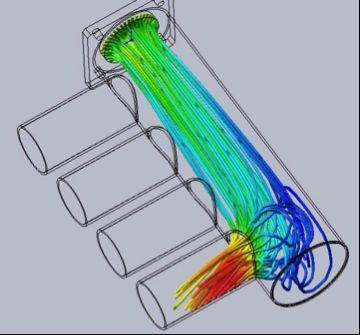
Exemple de modélisation SEF
Matières premières, catalyseurs, vapeurs, produits finis – tous ces fluides se déplacent et s’écoulent. C’est pourquoi une raffinerie ou une usine pétrochimique devrait se préoccuper de la dynamique numérique des fluides (DNF), car ce procédé permet de simuler, d’analyser et de résoudre les problèmes d’écoulement des fluides. La DNF utilise l’analyse numérique, les structures de données et les calculs informatiques pour modéliser l’écoulement des fluides et ses interactions avec les conditions limites.
Grâce à la modélisation DNF, nous pouvons comprendre des phénomènes complexes avec des informations simultanées sur la masse, la quantité de mouvement et le transfert de chaleur. Nous pouvons ensuite utiliser ces données pour planifier des tests avancés, valider et affiner les conditions limites et développer des solutions personnalisées.
Aperçu des tests
Depuis que l’unité de traitement a commencé à fonctionner à la mi-2019, nous avons effectué divers tests en utilisant plus de 50 capteurs pour l’étalonnage, et nous avons analysé de multiples balayages et images IR. Voici trois des résultats les plus intéressants :
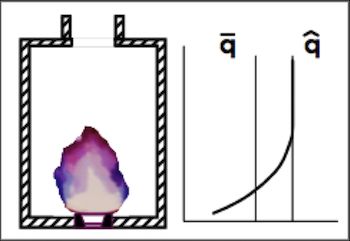
Distribution longitudinale typique du flux de chaleur
1- Répartition longitudinale typique du flux de chaleur dans un foyer vertical pour le chauffage au gaz
- La chaleur augmente et atteint un pic vers l’extrémité de la chambre de combustion (configuration symétrique).
- Les températures les plus élevées du tubeskin se situent normalement là où le flux de chaleur et les températures de process sont élevés.
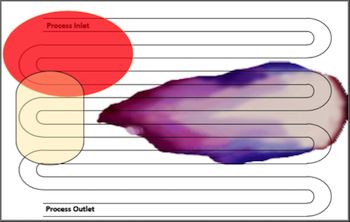
Symétrie le long de l’axe de tir
2- Chauffage de four à feu horizontal avec symétrie le long de l’axe de tir
Le flux de chaleur augmente sur la longueur, n’atteint pas son maximum à la ligne médiane et est biaisé vers la région supérieure. La compréhension des caractéristiques de l’équipement est la clé de la performance du four. Cela aide les spécialistes en température de WIKA à comprendre les meilleurs emplacements pour chaque test individuel. Cela permet également d’illustrer à quel point les fours de nos clients sont uniques. Toutes ces variations exigent un haut niveau d’expertise des fours pour tirer le meilleur parti d’un système de surveillance de la température.
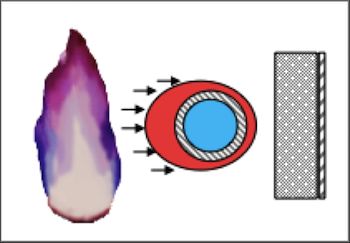
Distribution typique du flux thermique circonférentiel
3- Distribution circonférentielle typique du flux de chaleur dans un tube à feu unique
- La chaleur augmente et culmine vers l’axe du tube (configuration symétrique pour les tubes tournés vers la flamme).
- Sur le tube, les températures de peau les plus élevées sont normalement celles où se produit un flux de chaleur élevé et des températures de process élevées.
- L’emplacement spatial ainsi que circonférentiel est important lors de la mise en place du thermocouple.
Les clients au cœur de l’activité de WIKA
WIKA est un leader mondial de l’instrumentation, mais l’entreprise est bien plus que de simples produits. Car, comme on le sait, les capteurs et les manomètres ne suffisent pas à répondre aux besoins des clients. Notre objectif est d’utiliser nos produits pour résoudre des problèmes difficiles et fournir des solutions durables. Nous sommes votre partenaire axé sur les applications.
Cette nouvelle installation de test dans la région de Houston est simplement la dernière étape vers notre objectif d’anticiper et de satisfaire les besoins des utilisateurs finaux. Les résultats de laboratoire ont leur place et sont suffisants pour de nombreuses applications. Toutefois, les tests en situation réelle dans une unité de traitement à grandeur réelle produisent les données les plus fiables pour les applications pétrolières et gazières. Plus important encore, nous pouvons désormais reproduire – et non plus seulement simuler – vos problèmes, puis optimiser les solutions.