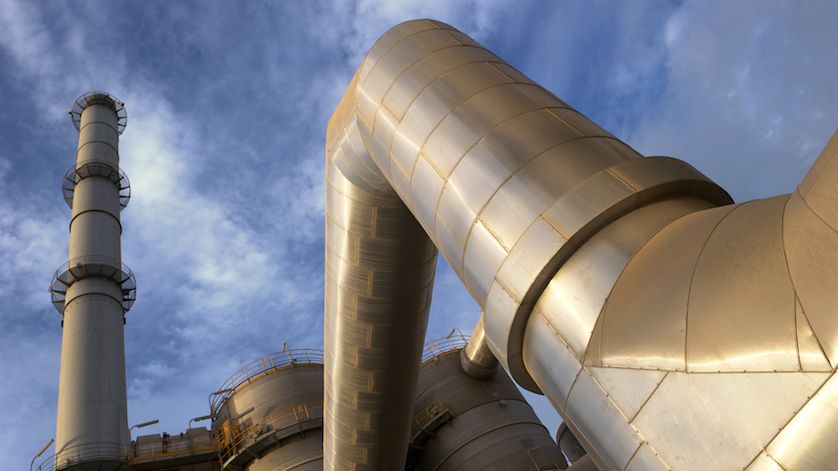
La récupération des gaz de combustion de faible niveau permet aux raffineries d’améliorer l’efficacité des fours. Toutefois, ce processus peut entraîner la condensation des gaz de combustion, et ces gouttelettes acides peuvent corroder les équipements. Pour une sécurité et une efficacité optimales, les raffineries doivent surveiller les températures et procéder à des ajustements opérationnels si nécessaire.
Dans les raffineries, les fours sont parmi les principaux consommateurs d’énergie, consommant environ 40 à 50 % du combustible dans les différentes unités de traitement. Le système de chauffage constitué de chaudières et de turbines à gaz consomme environ 30 à 40 % du combustible. Pour une raffinerie type dotée d’une installation de traitement secondaire, la consommation moyenne de combustible des fours s’élève à environ 7 % en poids du volume brut traité.
Avec la tendance croissante en faveur de la réduction des émissions de carbone, l’amélioration de l’efficacité des fours est l’une des mesures les plus importantes qu’une raffinerie puisse prendre. Une façon d’améliorer l’efficacité est d’utiliser la récupération de chaleur des gaz de combustion de faible niveau, qui consiste à échanger la chaleur des gaz de combustion avec des processus à plus faible température tels que l’eau d’alimentation des chaudières, l’air de combustion, etc.
Cependant, la récupération de chaleur des gaz de combustion de faible niveau comporte des défis, et l’un des plus importants à garder à l’esprit est la corrosion au point de rosée des gaz de combustion.
Condensation et corrosion dans les équipements de raffinerie
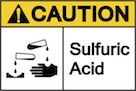
Plusieurs chercheurs ont effectué des travaux approfondis pour estimer avec précision le point de rosée acide, ou la température à laquelle un gaz acide se condense en gouttelettes. Pour les fours, l’objectif est de maintenir la température des zones sensibles au-dessus de ce point de rosée. Cette variable est facile à contrôler dans des conditions de fonctionnement normales. Cependant, dans les périodes de ralentissement, comme celle que connaît actuellement l’industrie, la zone de basse température des fours – communément appelée la partie froide – peut approcher la température du point de rosée acide.
Des débits plus faibles, des risques de corrosion plus élevés
Depuis que l’épidémie de la COVID-19 s’est répandue dans le monde, les consommateurs et les entreprises ont réduit leur consommation de carburants de transport. L’industrie pétrolière et gazière a répondu à cette baisse de la demande en diminuant la production des raffineries, les plus fortes baisses étant enregistrées dans les unités axées sur la production d’essence.
Selon l’Administration américaine de l’information sur l’énergie (EIA) : « Les apports bruts en UDA [unités de distillation atmosphérique] en avril 2020 étaient de 3,4 millions de barils par jour (b/j) (21 %) inférieurs à la moyenne des cinq dernières années (2015-19), et les apports bruts en UDA en mai 2020 étaient de 3,6 millions de b/j (21 %) inférieurs à la moyenne des cinq années (figure 1). Par rapport aux UDA et aux autres unités en aval, les entrées dans les craqueurs catalytiques, associées à la production d’essence dans une raffinerie, ont connu la deuxième plus grande variation en volume par rapport aux moyennes sur cinq ans en avril et mai, avec respectivement une moyenne de 1,6 million b/j et 1,4 million b/j de moins » (This Week in Petroleum, 19 août 2020, U.S. EIA).
Le fonctionnement à plus faible débit des fours a un impact direct sur les températures du point froid, ce qui pourrait entraîner une corrosion par point de rosée acide. Pour garantir un fonctionnement optimal et l’intégrité des équipements, les raffineries doivent surveiller les températures et procéder à des ajustements opérationnels si nécessaire.
Les points froids dans les fours d’air
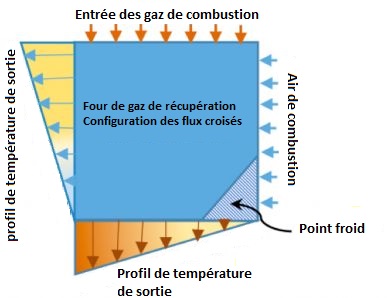
Figure 1 : Profil d’un four d’air à récupération (APH
De tous les équipements composant un four, les plus sensibles à la corrosion par point de rosée acide sont les fours d’air (APH). Ces échangeurs de chaleur transfèrent la chaleur des gaz de combustion à l’air de combustion avant qu’il n’entre dans le brûleur. Pour ce faire, la plupart des récupérateurs APH sont disposés dans une configuration d’écoulement de haut en bas et d’un côté à l’autre (figure 1).
Cette configuration crée des gradients de température du côté des gaz de combustion et de l’air de combustion de l’APH, créant ainsi un point froid à l’emplacement correspondant à la plus basse température des gaz de combustion et de l’air de combustion.
Mesure de la température dans les fours d’air
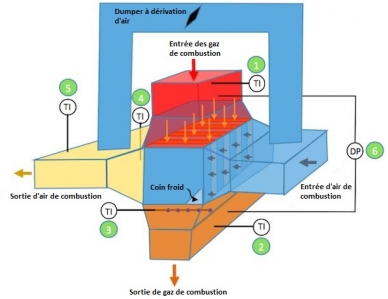
Figure 2 : Instrumentation et configuration typiques d’un récupérateur APH, et emplacements des indicateurs de température (TI) et du transmetteur de pression différentielle (DP)
Normalement, dans un APH, la température des gaz de combustion mélangés en aval est utilisée pour la surveillance et les ajustements opérationnels. Toutefois, elle est utilisée avec des marges pour pouvoir établir une corrélation avec les températures minimales du métal des tubes au point froid.
Dans la figure 2, ① et ② montrent les emplacements habituels d’un indicateur de température des gaz de combustion (TI). Cependant, à mesure que l’APH vieillit et s’encrasse le profil de température spatial change en raison des modifications des caractéristiques de transfert de chaleur. Ce changement peut ne pas être apparent à partir d’une mesure de température en un seul point.
La plupart des raffineries savent déjà qu’elles peuvent utiliser la surveillance de l’état des fours pour éviter l’encrassement, les fuites, la répartition des flux et d’autres problèmes de performance. Alors que les débits sont actuellement plus faibles, les raffineries doivent également tenir compte de la condensation du point de rosée acide dans les équipements sensibles. Dans un APH, une façon de le faire est d’actionner le registre de dérivation de l’air. Il est également important de mesurer le profil de température à la sortie des gaz de combustion ③, ainsi que de surveiller la pression différentielle (DP) avec un transmetteur DP sur le site ⑥ – du côté des gaz de combustion.
Dans la plupart des APH, la mesure de la température de l’air de combustion se fait uniquement sur ⑤ : le conduit combiné au brûleur après le by-pass. Cela est suffisant pour les conditions où le by-pass côté air est entièrement fermé. Toutefois, ce seul emplacement ne fournit pas d’informations sur les performances des APH lorsqu’une partie de l’air vers l’APH est contournée, ce qui est généralement le cas lors du fonctionnement dans des conditions ralenties. C’est pourquoi la mesure de la température de l’air de combustion avant et après la dérivation (point ④) est très utile pour le diagnostic et l’évaluation des performances.
WIKA, un leader mondial dans les technologies de mesure
WIKA est un pionnier dans le domaine de la mesure de la température électronique (ETM) et des solutions de mesure de pression pour l’industrie du raffinage et de la pétrochimie.
WIKA peut vous aider à surveiller l’état des fours et à prévenir la condensation/corrosion acide. Contactez nos spécialistes si vous souhaitez savoir si votre raffinerie pourrait bénéficier d’une surveillance avancée de votre APH et d’autres équipements.