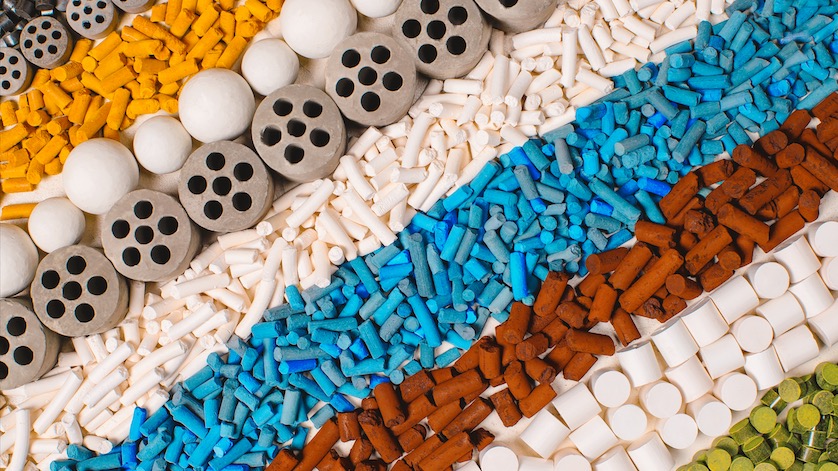
Un important producteur de catalyseurs n’était pas satisfait de la courte durée de vie des capteurs de température dans ses calcinateurs rotatifs. WIKA a proposé une solution innovante qui protège les thermocouples des dommages mécaniques tout en fournissant des mesures précises et un temps de réaction rapide.
Les catalyseurs sont un élément essentiel des activités pétrolières et gazières, notamment la production de gaz de synthèse et lors des process de raffinage tels que l’hydrocraquage et le craquage catalytique fluide (CCF). La fabrication de produits alimentaires, pharmaceutiques, chimiques et pétrochimiques repose également sur les catalyseurs.
Le rôle des catalyseurs
Disponibles sous une multitude de formes et de formulations, les catalyseurs sont des substances qui accélèrent et optimisent les réactions chimiques en abaissant leur énergie d’activation. En utilisant un catalyseur, les températures et les pressions ne doivent pas être aussi élevées, ce qui permet aux fabricants d’économiser beaucoup de temps et d’énergie. Ils peuvent être remis en service après avoir été traités à la chaleur, à l’hydrogène, dans des solutions acides ou alcalines, ou par un autre process de régénération, même s’ils devront être remplacés à un moment.
La plupart des centaines de catalyseurs utilisés dans la fabrication sont des catalyseurs supportés, dans lesquels le composant actif, tel qu’un métal ou un oxyde métallique, est lié à un substrat porteur. Les matériaux de support comprennent l’alumine, le charbon actif, la céramique, divers polymères, la silice, la zéolithe et la zircone. Les supports idéaux sont :
- Poreux, de sorte que le catalyseur dispose d’une grande surface sur laquelle il peut se déposer, car plus il y a de matériau catalytique, plus il y a de rencontres avec les molécules du réactif.
- Purs et inertes, afin de ne pas créer de réactions chimiques secondaires
- Mécaniquement solides, car un matériau dur résiste mieux aux process industriels et à la régénération des catalyseurs.
Les catalyseurs sur support sont généralement produits par calcination dans des fours rotatifs, également appelés calcinateurs rotatifs.
Comment les catalyseurs sont fabriqués dans les calcinateurs rotatifs
La calcination, en particulier dans un calcinateur rotatif, n’est que l’une des nombreuses étapes de la production de catalyseurs en grandes quantités. La méthode de fabrication spécifique dépend du type de catalyseur fabriqué. En général, ces étapes sont les suivantes.
- Préparation des matières premières : Des particules de céramiques, de métaux et/ou de polymères sont mélangées à une solution pour créer une suspension de catalyseur et de matériaux de support.
- Traitement hydrothermique : La suspension est versée dans un réacteur, où elle est chauffée et agitée jusqu’à ce que le matériau de support soit imprégné d’atomes de catalyseur. Le réacteur sèche ensuite les cristaux obtenus jusqu’à ce qu’ils atteignent l’état de poudre.
- Mise en forme : La poudre est mélangée à un agent liant et la pâte obtenue est généralement introduite dans une extrudeuse. Ce précurseur de catalyseur peut également être mis sous forme de pastilles ou de tablettes. La taille et la forme de la pâte ont un impact sur ses performances et sa résistance structurelle.
- Calcination : Les catalyseurs façonnés sont introduits dans un calcinateur, un four qui applique une chaleur élevée pour sécher et durcir le matériau et brûler les impuretés. La calcination peut également modifier la phase du catalyseur, augmenter sa surface et/ou l’activer. Un calcinateur rotatif assure une agitation continue au fur et à mesure que le catalyseur descend dans la cuve tournante et est exposé à des températures de plus en plus élevées, ce qui permet d’obtenir un produit de meilleure qualité et plus uniforme.
- Réduction : Une fois calciné, le catalyseur peut passer dans une atmosphère réductrice pour éliminer l’oxygène de l’oxyde métallique. Cela permet de s’assurer que le catalyseur est dans un état correct.
- Activation : Si la calcination n’a pas suffisamment activé le catalyseur, l’étape suivante consiste à le traiter avec un réactif.
- Conditionnement : maintenant pur et prêt à l’emploi, le produit final est placé dans des fûts, scellés pour éviter toute contamination, puis expédiés au client.
Problème : Mesure de températures élevées dans les conditions difficiles d’un four rotatif
Les fours rotatifs industriels permettent de calciner efficacement de grandes quantités de catalyseurs. Les capteurs de température sont essentiels à cette étape, car le traitement thermique approprié des catalyseurs exige une surveillance et un contrôle précis de la température. Les données sont transmises à un système de contrôle informatisé, qui ajuste le débit d’air et l’apport de combustible en fonction des besoins, afin de maintenir des conditions de traitement thermique optimales.
Les calcinateurs rotatifs présentent une combinaison de défis de mesure que l’on ne retrouve pas dans beaucoup d’autres applications :
- Les températures peuvent atteindre 1 000°C, ce qui réduit la durée de vie des capteurs qui ne sont pas conçus pour des conditions aussi extrêmes.
- Les granulés de catalyseur durcis, lorsqu’ils sont projetés par le tambour en rotation, heurtent de manière répétée la sonde de température et l’endommagent au fil du temps.
- La plupart des sondes de température sont insérées individuellement à travers la paroi de la cuve par l’intermédiaire de brides. Une cuve rotative pose des problèmes en termes d’emplacement du câblage.
L’usine américaine d’une société européenne spécialisée dans la catalyse et la technologie des process avait du mal à trouver une solution de mesure de température capable non seulement de fournir un profil de température précis de ses calcinateurs rotatifs à combustion indirecte, mais aussi de résister aux défis logistiques et liés au fluide de l’application. Dans la conception originale du four, les thermocouples ne répondaient pas aux attentes du client en matière de durée de vie, même si un doigt de gant protégeait chaque capteur.
Solution : Un assemblage innovant de Pipewell pour remplacer les brides individuelles
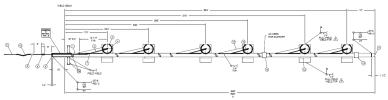
Assemblage de sondes de température conçu sur mesure par WIKA pour un calcinateur rotatif utilisé dans la production de catalyseurs.
WIKA et nos experts en température ont effectué une visite sur site pour examiner l’application. Le grand calcinateur rotatif, d’une longueur d’environ 18 mètres, était équipé de six capteurs de température à brides insérés sur toute la longueur de la cuve. Ils nous ont demandé si nous pouvions trouver une meilleure façon de mesurer les températures internes de l’unité tout en protégeant les capteurs des granulés de catalyseur durs.
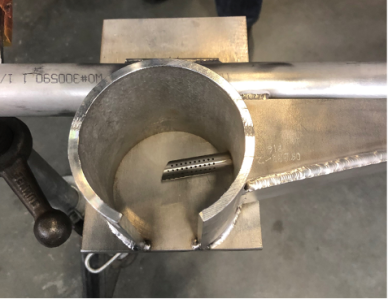
Coupe transversale de la chambre de protection semi-ouverte, montrant un tube d’insertion perforé
Pour éviter les problèmes liés aux capteurs à bride individuelle insérés dans la paroi de la cuve, nous avons décidé de créer un puits tubulaire spécial qui pénètre dans le four par une trappe à l’extrémité de l’entrée. Ce puits a été conçu avec une chambre de protection semi-ouverte. Six petits tubes ont été insérés régulièrement le long de ce puits, chacun étant perforé à l’extrémité pour permettre au catalyseur chaud d’entrer en contact avec le capteur tout en protégeant suffisamment les éléments sensibles fragiles. La partie du tube d’insertion qui ne se trouvait pas dans la chambre était protégée par une gaine.
Un thermocouple, dont le temps de réaction est plus rapide et la plage de température plus étendue que celle des sondes à résistance, a été inséré dans chaque tube perforé. L’utilisation de thermocouples isolés a permis d’obtenir un temps de réaction encore plus rapide aux changements de température, et l’utilisation du thermocouple connu de type K a permis d’obtenir une résistance à la corrosion, une sortie stable et une plage de température élevée – jusqu’à 1 260 °C – à un prix abordable. Le transmetteur de température numérique T32 de WIKA transmet les données de température au système de contrôle central de l’installation.
Résultat : Thermocouples à longue durée de vie pour les équipements de traitement thermique
Après l’installation de cet ensemble dans les calcinateurs rotatifs, les capteurs multipoints spécialement conçus ont surveillé sans faille les températures internes des unités. L’usine de catalyse a pu augmenter la durée de vie de ses capteurs de température de quelques mois à trois ans et plus, ce qui a permis de réduire considérablement les dépenses d’exploitation et d’améliorer la sécurité et l’efficacité grâce à une surveillance et à un contrôle précis de la température. Depuis l’installation de nos ensembles de température, le fabricant de catalyseurs a intégré cette conception dans les spécifications de son site.
WIKA, « Smart in Sensing » pour la fabrication de catalyseurs
Les spécialistes produits WIKA ont des décennies d’expérience dans la conception de solutions innovantes pour les défis de mesure les plus délicats. Nous travaillons en étroite collaboration avec nos clients pour comprendre leurs problèmes, puis nous concevons et installons des ensembles qui maximisent les opérations d’une usine, augmentent la sécurité et réduisent les dépenses. De plus, nous assurons un suivi régulier pour peaufiner l’assemblage, et nous fournissons des services de remplacement et d’installation lorsque les capteurs atteignent la fin de leur durée de vie naturelle.
Contactez-nous pour plus d’informations sur les solutions de capteurs pour les calcinateurs rotatifs et autres applications à haute température.