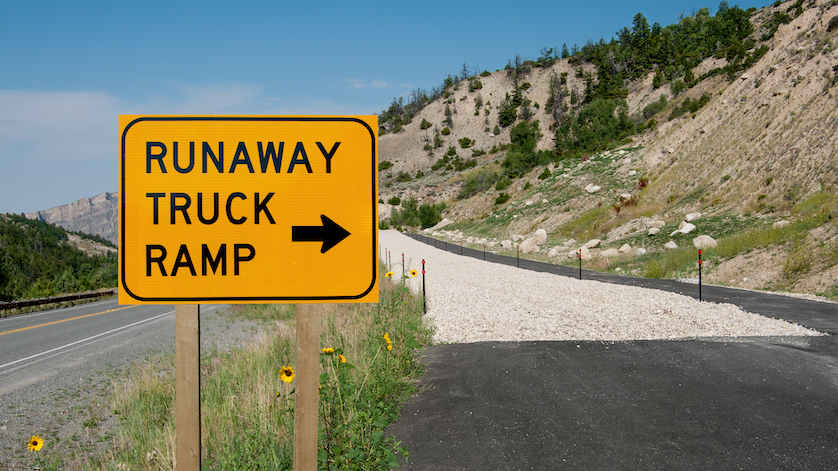
L’emballement thermique est l’une des principales causes d’accident dans les usines chimiques et pétrochimiques. Pour éviter de telles catastrophes, les opérateurs doivent surveiller en permanence les températures à l’aide de capteurs dont le temps de réponse est le plus rapide possible pour l’application concernée.
La fabrication de l’oxyde d’éthylène, de l’acide acrylique, du chlorure de vinyle, du styrène et d’autres produits importants implique des réactions hautement réactives et exothermiques.
Comme ces process chimiques produisent d’énormes quantités de chaleur, ils doivent être gérés avec soin pour éviter les augmentations rapides de température et les réactions d’emballement.
Les dangers de l’emballement des réactions chimiques
Si vous avez déjà conduit sur des routes de montagne, vous avez probablement rencontré des rampes d’emballement. Ces rampes en cul-de-sac utilisent une pente ascendante et/ou le frottement du gravier pour arrêter les camions qui ont perdu l’usage de leurs freins et sont incapables de contrôler leur véhicule alors qu’il dévale une route escarpée.
Il en va de même pour les réactions chimiques qui s’emballent. Il s’agit de process qui se sont tellement accélérés qu’ils deviennent très difficiles, voire impossibles à contrôler.
Dans les usines chimiques, les points à vérifier :
- Mesures de contrôle du process – abaisser la température et la pression en réduisant le débit de la matière première et en ajustant sa concentration.
- Techniques d’évacuation de la chaleur – telles que les chemises de refroidissement, les échangeurs de chaleur et les dispositifs de contrôle de la température.
Le danger survient lorsque ces mesures de sécurité sont insuffisantes ou inefficaces. Si un emballement de la réaction thermique n’est pas stoppé, il peut entraîner des explosions, des incendies, des dommages aux installations, des émissions toxiques, des blessures et des pertes de vies humaines. Et malheureusement pour les usines chimiques, il n’y a pas d’équivalent à une rampe d’emballement si les systèmes de sécurité ne parviennent pas à arrêter les process hors de contrôle.
Contrôler les réactions chimiques pour éviter les emballements
La maîtrise des réactions exothermiques dans une installation pétrochimique est un élément clé de la sécurité de l’usine. Prenons l’exemple de l’oxyde d’éthylène (OE). Le C2H4O est largement utilisé comme intermédiaire chimique dans la fabrication d’une large gamme de produits de tous les jours, des adhésifs et solvants aux détergents, textiles et produits pharmaceutiques. La fabrication de l’OE implique des réactions exothermiques à haute température et à haute pression, produisant un gaz incolore très réactif et inflammable.
Les réacteurs d’OE sont également très sensibles et toute perturbation peut entraîner l’emballement de ces unités. Les perturbations peuvent prendre la forme d’un bouleversement du process, tel qu’un dysfonctionnement ou une défaillance de l’équipement, une hausse ou une baisse des paramètres critiques, ou même la préparation d’une révision.
Le rôle des capteurs de température dans la prévention des réactions d’emballement
La gestion de la température d’une réaction est le principal moyen d’influencer sa cinétique. La température et la pression étant directement proportionnelles lorsque le volume est constant, abaisser la température d’une réaction revient à réduire également la pression à l’intérieur d’un récipient fermé. Les sondes de température, tels que les thermocouples et les thermomètre sondes à résistance (RTD), permettent aux opérateurs de surveiller en permanence la température des réactions chimiques exothermiques.
La température étant un paramètre essentiel dans les réactions exothermiques, qui peuvent s’emballer en quelques secondes, le temps de réponse d’un capteur joue également un rôle crucial dans la capacité de la salle de contrôle à prendre des décisions en connaissance de cause et à gérer efficacement le process.
Les producteurs de produits chimiques utilisent couramment des réacteurs tubulaires pour convertir les hydrocarbures en oxyde d’éthylène, en acide acrylique, en chlorure de vinyle et en styrène. Les capteurs de température sont adaptés à la conception spécifique d’un réacteur, avec des dimensions, des longueurs et un nombre de points de mesure variables.
Les instruments de mesure ne se contentent pas de collecter des données, ils font souvent office de mécanismes de sécurité qui déclenchent des alarmes lorsque les conditions du process dépassent des paramètres prédéterminés. Grâce à des redondances telles qu’un séparateur de secours, les capteurs utilisés dans des applications critiques empêchent la libération accidentelle de fluides en cas de défaillance mécanique.
Configurations de capteurs pour des relevés de température optimaux
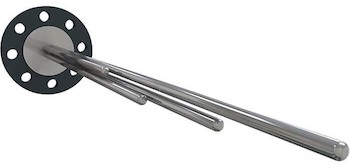
Thermocouple miniature multipoint TC96-M
Il existe différentes configurations de points de mesure de la température pour les réacteurs tubulaires. Pour obtenir les résultats les plus précis, il convient d’utiliser des thermocouples miniatures multipoints, comme le thermocouple TC96-M, afin de détecter rapidement tout changement de température soudain sur la longueur du réacteur. Ces capteurs sont connectés à un transmetteur de température pour transmettre rapidement les données à la salle de contrôle.
Considérations et compromis en matière de détection de la température
Pour garantir l’intégrité et la fiabilité du réacteur, les capteurs de température doivent avoir un temps de réponse rapide. Moins il y a de matière entre la pointe du capteur et le milieu, plus le temps de réponse est rapide.
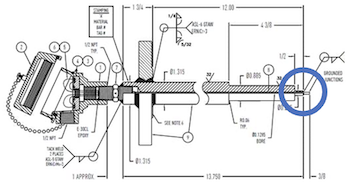
Thermocouple dans un doigt de gant à pointe exposée
Par exemple, un thermocouple non isolé est inséré dans un doigt de gant à pointe exposée (voir à droite), de sorte que le capteur entre en contact direct avec le gaz ou le liquide. La contrepartie, bien sûr, est que si le milieu est agressif ou extrêmement chaud, cette configuration peut réduire considérablement la durée de vie du capteur de température.
En résumé, voici quelques-unes des variables qui influencent les temps de réponse thermique des sondes de température :
- Le type de capteur de température. En général, les thermocouples ont un temps de réponse plus rapide que les RTD.
- La taille du capteur. Plus le capteur est petit, plus son temps de réponse est rapide.
- La nécessité ou non d’un doigt de gant. Ce tube métallique protège le capteur des hautes pressions, des températures élevées et des milieux abrasifs/corrosifs.
- L’épaisseur de la paroi du doigt de gant. Plus la paroi est fine, plus le temps de réponse est rapide, mais l’intégrité structurelle d’un doigt de gant à paroi fine peut être affectée dans des conditions de vitesse élevée et de turbulences.
- Le diamètre de l’extrémité du doigt de gant. Moins il y a d’air entre la pointe du capteur et la paroi du doigt de gant, plus le temps de réponse est rapide.
- Le type de fluide. Les fluides liquides auront un temps de réponse plus rapide que les fluides gazeux en raison du contact plus important du liquide avec la surface de mesure.
- La vitesse et turbulence du fluide. En général, les fluides plus rapides et plus turbulents entraînent des temps de réponse plus rapides en raison d’un contact plus important avec la surface de mesure.
A l’aide de conseils d’experts et de capteurs de qualité, WIKA aide ses clients industriels pour prévenir les réactions d’emballement
Lors du choix des instruments de température pour surveiller les process d’un réacteur, la meilleure pratique n’est pas d’utiliser simplement le capteur avec le temps de réponse le plus court. Pour trouver l’équilibre parfait entre le temps de réponse et la résilience du process, il faut faire appel à des spécialistes des produits ayant l’expérience de l’industrie chimique.
Nous pouvons vous conseiller sur l’utilisation d’une sonde de température ou d’un thermocouple, et vous indiquer si le capteur de température peut être inséré directement dans le fluide ou s’il doit être utilisé avec un doigt de gant. Dans ce dernier cas, nous pouvons vous aider à effectuer les calculs de stress pour protéger les doigts de gant des contraintes mécaniques. Un doigt de gant à profile hélicoïdal, comme notre modèle ScrutonWell®, minimisera les formations de sillage qui endommagent la gaine d’un doigt de gant et permettent au fluide de s’échapper dans l’environnement.
Pour que votre installation fonctionne de la manière la plus sûre et la plus efficace possible, travaillez avec les experts de WIKA pour des solutions de température optimisées pour vos réacteurs et process spécifiques.